TECHNOLOGY
技術・開発
熱交換器管端溶接部フェーズドアレイ
超音波探傷検査システム
日立造船株式会社との共同開発
本システムが、2019年度 第50回日本溶接協会賞の「第35回溶接注目発明賞」を受賞しました。
システムの概要
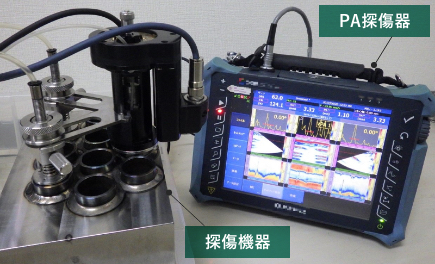
図1)フェーズドアレイ超音波探傷検査システムの構成
石油精製や石油化学等のプラントに用いられる熱交換器は、気体や液体など異なる流体の熱交換を行う機器であり、機器胴体、熱交換を行う管と管を固定する管板が主要な構造となっています。
管と管板を接合する管端溶接部は、溶接部の表面など目視可能な範囲を対象とした非破壊検査により溶接欠陥の有無を確認しますが、管端溶接部の内部においても非破壊検査できるフェーズドアレイ超音波探傷検査(PAUT)システム(図1)を開発しました。
フェーズドアレイ技術は、複数の振動子を連続的に振動させることで、従来のUTでは実現できなかった特殊なビーム走査が可能です。この技術により、欠陥検出性能の向上と検査時間の削減を実現します。
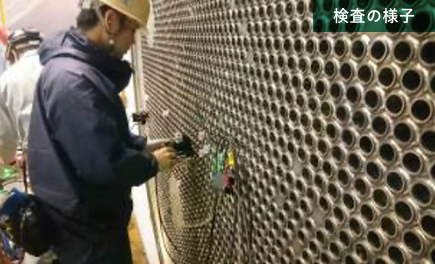
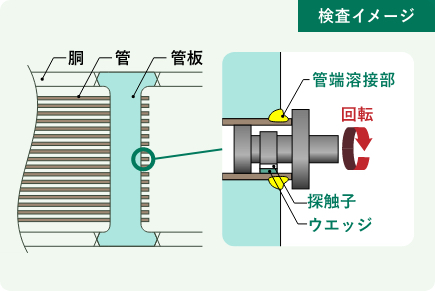
図2)管端溶接部の検査
本システムは、管内部に探傷機器を挿入・回転させ、溶接欠陥の有無や溶接金属の高さを測定することが可能です(図2)。
ディープラーニングの活用
また、取得した探傷データを判定するためにAI(人工知能)技術であるディープラーニングを活用して溶接欠陥の有無を精度良く自動判定(識別)します。
これまでの管端溶接部の検査では、例えば約200 万枚の画像データを検査員が目視で判定していました。その場合、300 時間に及ぶ判定時間と労力を要していましたが、ディープラーニングを活用した異常検知技術によって溶接欠陥の見落としを無くし、大幅な業務効率化と判定精度の向上を実現しています。
従来の検査の場合
Step.1
管端PAUT装置
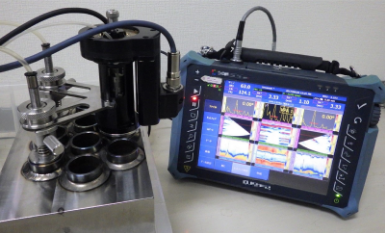
Step.2
探傷画像を取得
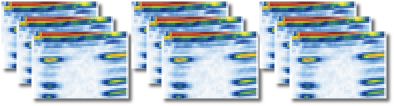
STEP.3
検査員による目視確認
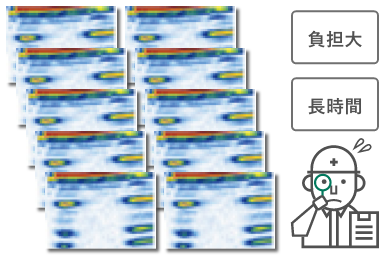
検査員の負担が大きく、検査時間が長時間必要
自動判定システムを適用した場合
Step.1
管端PAUT装置
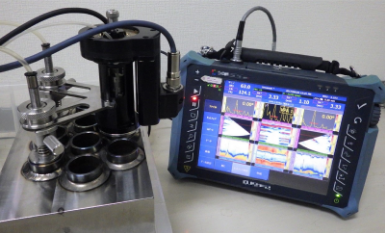
Step.2
探傷画像を取得
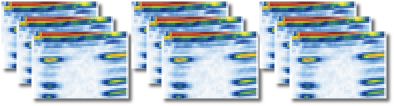
STEP.3
検査員による目視確認
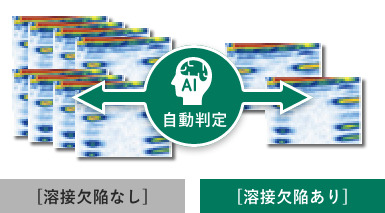
ディープラーニングを活用した自動判定
判定精度は管単位99%以上
STEP.4
検査員による目視確認
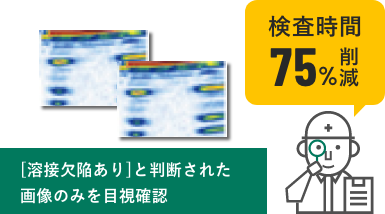
目視画像枚数が大幅に削減され、
検査員の負担軽減
アワードの受賞
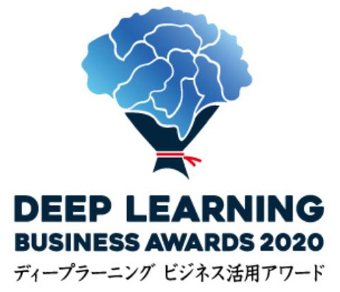
日立造船株式会社は、本システムがディープラーニングを活用した優れたプロジェクトとして、
大手経済誌主催の「第2回ディープラーニングビジネス活用アワード」で大賞を受賞しました。
これは、本システムの高い技術力とディープラーニングを組合せたことによるビジネス活用の成果、そして一般に適用が遅れている非破壊検査の分野で開発に挑み、ディープラーニングを活用することによってものづくりが変革できた点が高く評価されました。
当社は、非破壊検査機器の設計・製作およびディープラーニングを含む解析ソフトウェアの開発に大きく貢献しています。
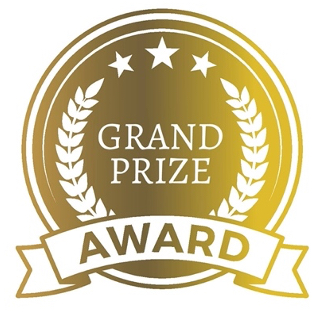
本システムは、熱交換器の製造時検査やプラントにおける定期検査で活躍しています。
製造時検査では管端溶接部に内在する欠陥の有無と発生位置を報告し、お客様へ納品する熱交換器の品質向上に貢献しています。
定期検査では腐食による管内表面の凹みや欠陥の発生位置、応力腐食割れの有無などを検査翌日に報告しており、お客様からご好評いただいております。
引き続き、様々な熱交換器の管端溶接部検査を通じて、プラントの安定稼働やメンテナンスの業務効率化に貢献します。
参考
- 熱交換器の管端溶接部非破壊検査システム,Hitz技報,第77巻,48-49 (2016)
- ULTRASONIC TESTING AND PHOTOGRAPHIC IMAGING SYSTEM FOR TUBE TO TUBESHEET WELD OF HEAT EXCHANGER,ASME PVP2017-65569
- 多管式熱交換器における管端溶接部のPAUT検査技術,溶接構造シンポジウム2019 講演論文集,38s-43s (2019)
- 管端溶接部の溶接欠陥有無自動判定システムの開発,Hitz技報,2020,81(1), 2-8.